Waterproof connectors are used in waterproof quick connectors for connecting wires and cables of new optoelectronic technology products such as LEDs and guardrail tubes. They are mainly used in outdoor waterproof and moisture-proof. In short, waterproof connectors can be applied to environments with water. Under the condition of certain water pressure, the connector can ensure the normal use of the internal mechanical properties and electrical properties of the connector, so as to ensure the safe use of electricity for equipment interoperability.
In industrial environments, such as LED lighting, urban outdoor lighting projects, lighthouses, cruise ships, aviation, industrial equipment, cables, sprinklers, etc., waterproof connectors are required. Due to the strict application requirements in the military field, a large number of waterproof connectors are used, such as connectors for submarines and connectors for submarine-launched missiles.
First, first of all, it meets the requirements of relevant electrical, installation, connection, insulation, protection and other technical standards, which is the basis for selection.
Second, you can‘t just look at the standard, you should go beyond the standard and pay attention to the situation encountered in practical application.
Because some of the standards selected for the design and production of connectors in the LED industry are actually borrowed from other industries, because the industry application time is relatively short, many terms do not meet and meet the rapidly changing requirements of the LED industry, such as the requirements for aging-resistant materials. The assessment is only generally in line with the use of outdoor projects, but how to define it depends on whether it is based on the UL yellow card or the test. The lifespan shall prevail", which directly affects the selection and design of product materials, and is also the reason for the variety of LED connector materials.
In addition, the requirements of individual standard clauses are still relatively low, that is to say, the threshold for quality is very low, resulting in all kinds of home workshops can be produced at will, and some test standards are tested in a "standard static environment", which often occurs After the engineering accident, the connector was re-tested and found that it was still qualified according to the standard. Why? Because the laboratory tests have selected standard terms and standard environments, and the environment of the application site is very different, such as the cable gland at the end of the connector. Grasp the cable For the requirements of force and torque resistance, the standard only says that the tensile force reaches 60N, and the anti-torque value is greater than 0.3N.m, but the connector may be pulled and twisted artificially in actual use, so the actual data may be far from the standard value, and this The force is maintained between the two connectors for a long time. After a long time of outdoor use, the connector is often not waterproof or the contact is poor and the circuit is broken.
Third, look at the production quality control system of the connector manufacturer.
It is easy for a connector company to provide a pair of connectors for testing, and you can get good test scores, but when you arrive at the factory, you will find that there are no inspection standards for raw materials, and there is no necessary testing link for finished products. Repair and testing of unqualified products No procedures, etc., have affected the overall quality of the product, that is to say, only 100% qualified, not 1,000,000,000 qualified. In the long run, good quality system control is even the most important reference factor for lighting manufacturers to choose connector manufacturers, otherwise it will be "small loses big". In general, enterprises with larger production scale and technical testing equipment have a correspondingly higher level of product quality control and stability.
Fourth, look at the structural principle design, the structural design is very important.
If the principle design such as waterproofing and connection is more advanced, it will be better than others. If you choose an outdated structural principle design, even if the quality control in the manufacturing process is very good, it is often in reliability and outdoor long-term weather resistance. Sex and other aspects are not as reliable as the innovative generation of products.
Fifth, look at the tolerance size control accuracy of the assembly.
Because connectors often involve connection, waterproofing, male-female contact and mating, etc., they need to have high precision requirements for size. At first glance, high-end and low-end connectors are almost the same in shape and structure. How to spend some time and carefully measure the mating size of multiple pairs of connectors with a caliper, you will find that the mating size of poor quality varies greatly, that is, the stability of the connection is not guaranteed, and the consistency of batch products is poor.
Various parameters of waterproof connector
MaterialMaterial
Housing Housing: Nylon
Connector Conductor: Copper Brass
Rated output Rated power: 24A/32A 450VAC
Protection class IP code: IP68
Wiring Core: 2P/3P/4P/5P/6P
Working temperature: T105
Wiring range Rated connecting capacity: 0.5 ~ 4.0mm2
Applicable cable diameter (rubber cable) Available cable diameter (Roubber): 3-6mm 4-8mm 6-11mm 10-14mm
Waterproof Testing: 20M 150hours
Certification: ,ETL,ENEC,UKCA,CE,CB,SAA,ROHS
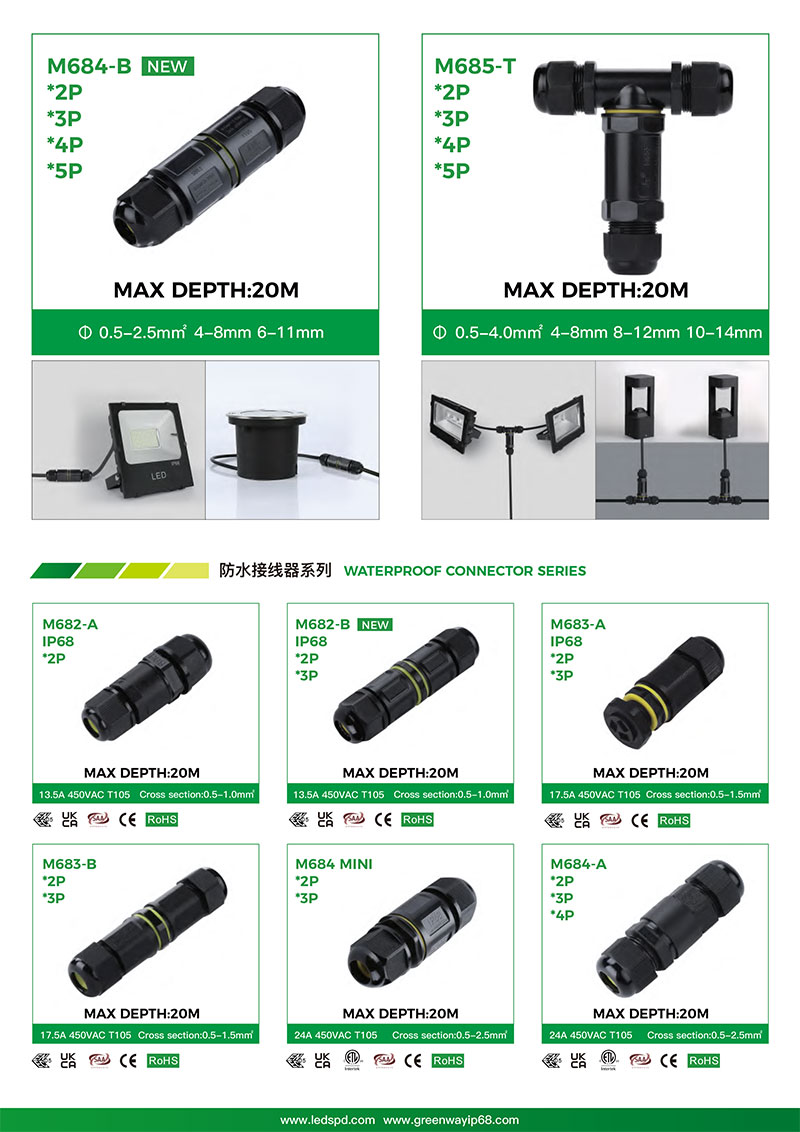
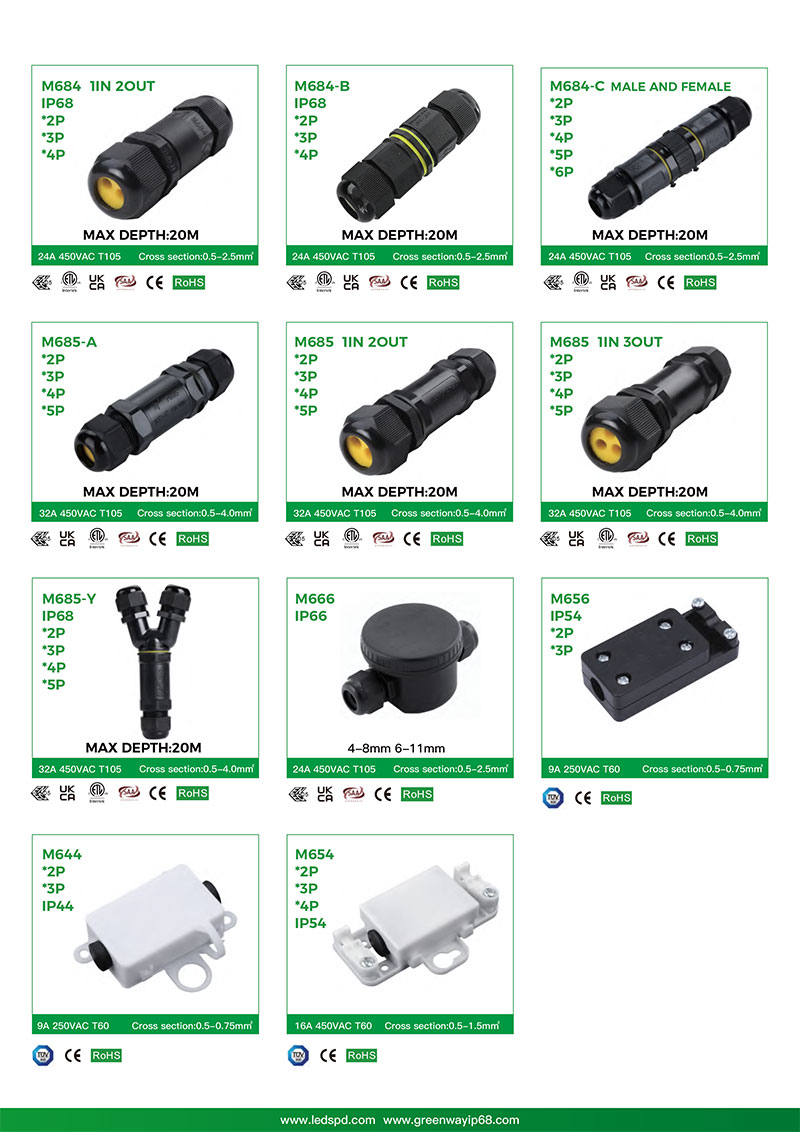